Understanding Concrete Mixing Plants: A Comprehensive Guide
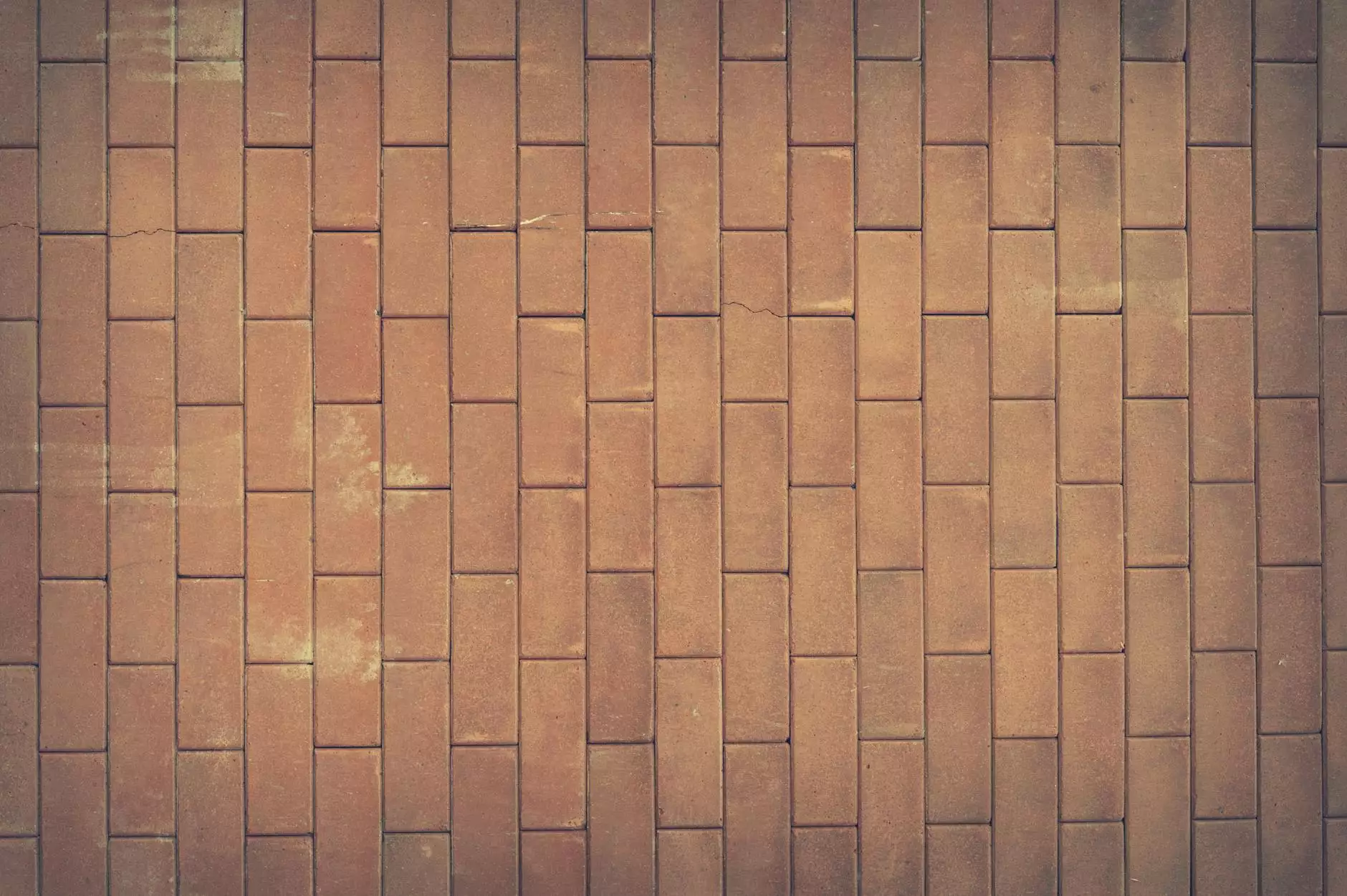
Concrete mixing plants are pivotal assets for the construction industry, streamlining the production of concrete—a critical building material. The importance of this machinery transcends simple mixing; they offer a blend of efficiency, precision, and adaptability.
What is a Concrete Mixing Plant?
A concrete mixing plant is an industrial facility designed for the mixing of different components needed to create concrete. These components typically include:
- Cement
- Water
- Aggregates (sand, gravel, etc.)
- Additives (to enhance performance)
Concrete mixing plants can vary in size and complexity, ranging from small, portable units to large, stationary installations catering to extensive construction projects.
The Importance of Concrete Mixing Plants in Construction
As urbanization continues to rise, the demand for concrete increases. Concrete mixing plants facilitate this demand by ensuring consistent quality and quantity of concrete, leading to several benefits:
1. Consistency and Quality Control
The precision with which materials are measured in a concrete mixing plant ensures that each batch of concrete meets the required specifications. This consistency is crucial for maintaining structural integrity and performance.
2. Efficiency in Production
Modern concrete mixing plants are designed to optimize time and resources. Automated processes streamline operations, reducing manual labor and minimizing errors, thus enhancing overall production efficiency.
3. Scalability
Concrete mixing plants are highly adaptable. Depending on the project requirements, a mixing plant can scale its production volume, allowing it to cater to both small residential projects and massive commercial developments.
Types of Concrete Mixing Plants
Understanding the different types of concrete mixing plants is essential for selecting the right one for specific construction needs. They can be categorized as:
1. Stationary Concrete Mixing Plants
These plants are fixed installations often used in large construction sites where massive amounts of concrete are required. They provide high production capacity and are equipped with advanced technological solutions.
2. Mobile Concrete Mixing Plants
Mobile plants are portable and can be quickly deployed to different job sites. They are ideal for projects that require flexibility and lower production volumes. The ease of setup makes them a favorite for many contractors.
3. Compact Concrete Mixing Plants
These plants offer a balance between stationary and mobile solutions. Compact plants are designed to occupy less space while still being able to produce significant batches of concrete, making them suitable for various job sites.
Key Components of a Concrete Mixing Plant
A typical concrete mixing plant consists of several critical components that work together to create high-quality concrete:
- Batching System: This system is responsible for accurately measuring and batching the various ingredients before mixing.
- Mixer: The heart of the plant, the mixer blends all components to ensure uniformity. Types of mixers include drum mixers and twin-shaft mixers.
- Control System: A sophisticated control system manages the entire process, ensuring precision and real-time monitoring of different parameters.
- Storage Units: These are used to hold ingredients such as aggregates, cement, and additives until they are needed for production.
- Conveying Systems: These systems transport materials between components of the plant, streamlining the mixing process.
Advantages of Using Concrete Mixing Plants
The advantages of employing concrete mixing plants cannot be overstated. Here are some significant benefits:
1. Enhanced Productivity
Concrete mixing plants can produce large volumes of concrete rapidly, significantly improving project timelines and efficiency.
2. Cost-Effectiveness
By centralizing mixing processes, concrete plants reduce transportation costs and raw material wastage, delivering significant savings over time.
3. Customization
These plants can be tailored to adjust concrete formulations as per specific project requirements, allowing for customized solutions that enhance performance and sustainability.
The Role of Technology in Concrete Mixing Plants
With the advent of technology, concrete mixing plants have evolved significantly. Key technological advancements include:
1. Automation and Control Systems
Modern plants utilize automated systems that maximize operational efficiency, minimize human error, and streamline the mixing process. This technology provides unparalleled control over concrete production.
2. Integration with IoT
Internet of Things (IoT) technologies enable remote monitoring and management of concrete mixing plants, providing real-time data and analytics that can drive informed decision-making.
3. Environmentally Friendly Solutions
Advanced technology also embraces sustainable practices, with equipment designed to minimize noise and dust emissions while optimizing energy consumption.
Maintenance of Concrete Mixing Plants
Regular maintenance of a concrete mixing plant is crucial for ensuring longevity and consistent performance. Key maintenance practices include:
- Routine Inspections: Conducting regular checks for wear and tear on equipment can prevent major breakdowns.
- Calibration: Ensuring that batching and mixing equipment are correctly calibrated is vital for maintaining consistent quality.
- Cleaning: Regular cleaning of the plant components prevents contamination and promotes smooth operations.
Challenges Faced by Concrete Mixing Plants
While concrete mixing plants offer numerous advantages, they are not without challenges. Some common issues include:
1. Regulatory Compliance
Meeting local regulations regarding environmental standards and operational safety can pose challenges for plant operators.
2. Material Quality Variability
The quality and availability of raw materials can fluctuate, impacting the overall consistency of concrete produced.
3. Technology Adaptation
As technology continues to evolve, plant operators must stay updated with the latest systems and techniques to maintain competitiveness.
The Future of Concrete Mixing Plants
Looking ahead, the future of concrete mixing plants is promising with the following trends:
1. Increased Automation
As automation technology advances, we will see even more sophisticated mixing plants capable of producing higher quantities with less human input.
2. Sustainable Practices
Emphasis on sustainability will drive innovation in manufacturing techniques, aiming for reduced carbon footprints and increased recycling of materials.
3. Enhanced Data Analytics
Big data and analytics will enable precise monitoring and forecasting, thereby enhancing operational efficiency and forecasting demand with higher accuracy.
Conclusion
In summary, concrete mixing plants play an indispensable role in the construction industry, providing not only efficiency but also quality and reliability. With continued advancements in technology and practices, these plants are poised to become even more integral to sustainable development and innovation in the built environment. Understanding their components, functions, and future outlook will help stakeholders make informed decisions and optimize their operations.
Explore Our Solutions at Polygon Machinery
If you are looking for top-of-the-line concrete mixing plants, visit us at Polygon Machinery. Our commitment to excellence ensures that you receive only the best equipment tailored to your needs.